石墨烯是一种由碳原子紧密堆积在一起所构成的二维蜂窝格子结构,是构成其它石墨材料的最基本结构单元。由于其结构中存在长程π-π结合键,石墨烯具有较高的比表面积、力学性能和室温电子迁移率,从而在电子、储能、生物医学等领域得到了极大的关注[1,2,3,4,5]。
近年来,石墨烯在各行各业飞速发展,但大部分科学研究成果仅局限于实验室中[6,7,8,9,10]。自2015年以来,《十三五规划纲要》、国家发改委等部门联合下发的《关于加快石墨烯产业创新发展的若干意见》,以及国务院发布的《中国制造2025》等文件中,都明确表明了石墨烯在中国前沿材料未来发展中占据的重要地位[11]。目前,石墨烯工业化生产还处于一个初步发展的阶段,仅有少数企业具备石墨烯粉体百吨级产量水平。并且,目前大部分石墨烯相关产品性能不达标、生产不稳定、重复率低,所以对产品的相关检测尤为关键。其中,石墨烯结构和粒径大小的不同会对其性能产生显著影响。已有研究表明,环氧树脂与大粒径石墨烯复合后的材料的热导率大于与小粒径石墨烯复合后的材料[12,13]。材料粒度检测至今已经有大量检测方法,主要为筛分法、沉降法、电阻法、电镜法、超声法、质谱法、光脉动法和激光法等[14,15]。
激光粒度分析仪可用于检测在液体或气体中分散的粉体材料的粒度分布。激光粒度分析仪工作中激光照射到微粉颗粒表面,发生衍射效应,不同大小的微粉颗粒衍射角度不同,从而投影的大小也不同,其根据全量程米氏散射理论进行粒径分析[16,17,18,19,20,21]。激光粒度分析仪具有测试范围大、测试时间短、自动化程度高、重复性好、分辨能力强等特点,能完全统计出材料整体微分分布情况,并可从分布曲线和数据中准确提取所需的材料粒径情况。因此,利用激光粒度分析仪对石墨烯进行粒径检测分析具有一定的研究意义。
1 试验部分
1.1 试验试剂与原料
石墨(C,325目)(青岛华泰润滑密封科技有限责任公司);浓硫酸(H2SO4,98%,AR)(兴平市福晨化工科技有限公司);高锰酸钾(KMn O4,99.5%,AR)(成都市科隆化学品有限公司);双氧水(H2O2,30%,AR)(成都市科隆化学品有限公司)。
1.2 试验方法
氧化石墨烯(GO)的制备方法为氧化还原法,为适应其工业化生产,对生产工艺做出了相应的改进。首先在反应釜中添加一定比例浓硫酸、石墨和高锰酸钾,不断搅拌,待其反应完全后,再加入双氧水去除剩余高锰酸钾;将制备好的浆料通过压滤工序,去除浆料里的浓酸,制备成氧化石墨烯滤饼;再将滤饼重新加入纯水中分散成浆料,再次清洗物料中的酸和金属离子,进一步提升浆料的p H值;清洗后的浆料进行超声处理,制备成氧化石墨烯浆料;最后,氧化石墨烯浆料经喷雾干燥工序制备成氧化石墨烯粉体。取氧化石墨烯粉体和氧化石墨烯浆料作为试验样品,通过LS-909激光粒度分析仪对其粒径进行检测。
2 结果与讨论
2.1 预处理超声时间的影响
2.1.1 检测方法
纳微级粒径材料比表面积大,颗粒所带电荷、水分、范德华力等表面能相互作用,溶于溶液中极易团聚,颗粒越细,其表面能越大,越容易团聚。如将其溶液不经预处理进行粒径检测,测定结果可能产生相应误差。激光粒度分析仪测定纳微级粒径材料前,需先将其溶液进行超声预处理,达到分散、避免沉降的目的。目前,国内外没有关于激光粒度分析仪检测石墨烯材料预处理超声时间相关的国家标准、行业标准或企业标准,现为验证最佳预处理超声时间,为检测石墨烯粒径提供一个更准确的环境,设计以下试验进行验证。取7个不同生产批次的氧化石墨烯粉体,标记样品名为F1~F7,每种取样1 g,分别溶于300 m L去离子水中,配制成溶液。检测之前使用激光粒度分析仪配备的超声装置对溶液进行超声,每种样品分别进行3次预处理超声,超声时间分别为1 min、2 min、3 min,每次超声后对其进行3次粒径检测,取3次检测数据的平均值。
2.1.2 结果分析
将F1~F7,7种样品超声1 min、2 min、3 min后测定结果中的D50粒径(平均粒径)和D90粒径数据绘制成图,如图1~4所示。图1和图2为5种氧化石墨烯粉体样品分别经过3种预处理时间后D50和D90粒径数据。从图中可以明显看出,随着预处理超声时间的增加,样品的粒径总体呈缓慢下降趋势。说明样品溶液超声作用时间越长,氧化石墨烯粒子在溶液中团聚现象越少,氧化石墨烯溶液分散性越好,激光粒度分析仪测定粒径数据越准确。图3和图4为F6和F7样品的粒径测定数据,从这2个样品可以看出,预处理超声1~3 min,粒径测定数据趋势与图2和图3明显不同。超声3 min下粒径测定D90数据远大于超声2 min的数据,数值相差10倍左右。结合图5和图6的超声3 min粒径微分分布图可以看出,F6和F7图线包含2个峰值,说明有部分氧化石墨烯在超声时间增加的过程中出现了明显的变化,这个变化是由于氧化石墨烯粒子形状变化引起的。
图1 5种氧化石墨烯粉体样品超声1 min、2 min、3 min的D50粒径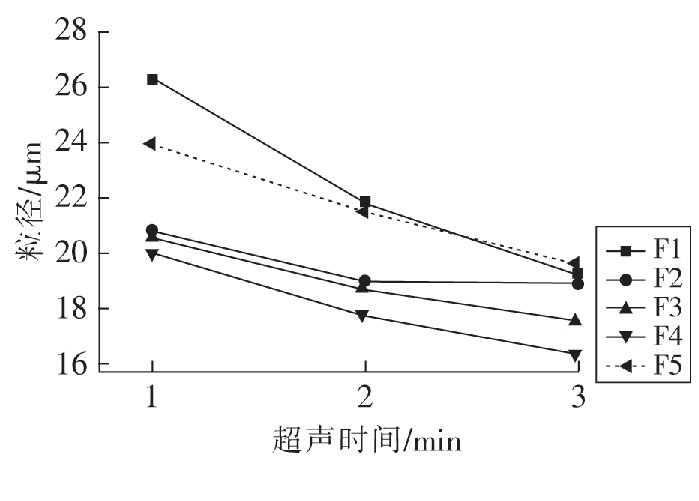
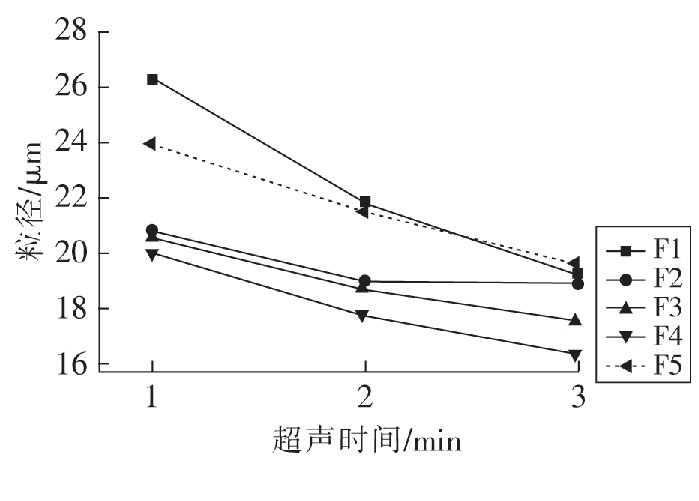
图2 5种氧化石墨烯粉体样品超声1 min、2 min、3 min的D90粒径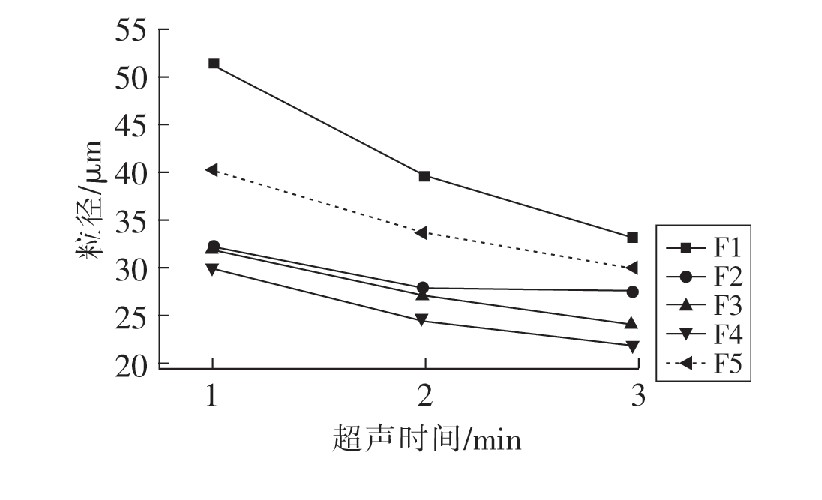
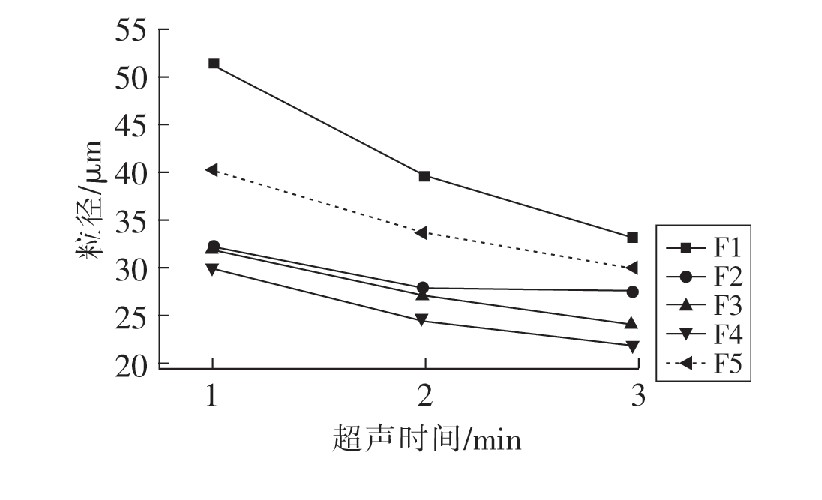
图3 F6和F7样品超声1 min、2 min、3 min的D50粒径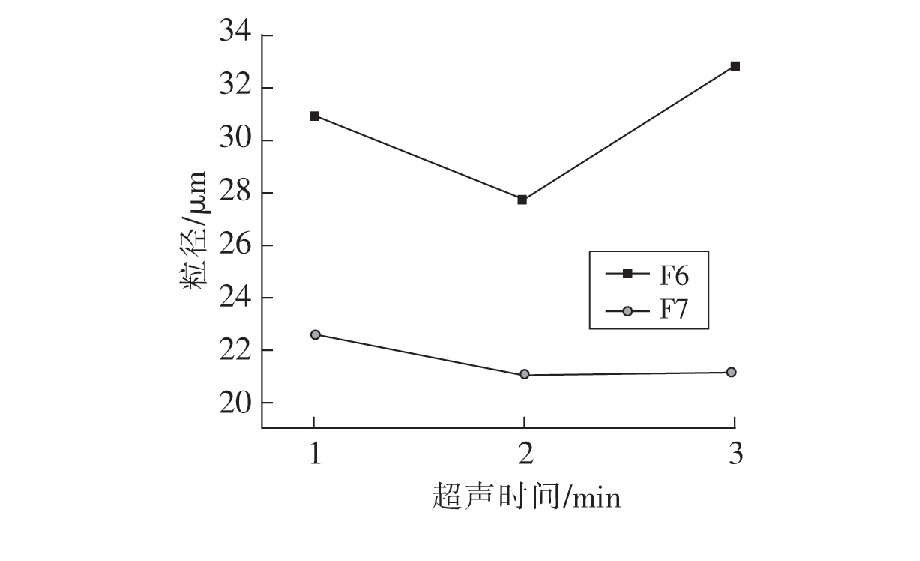
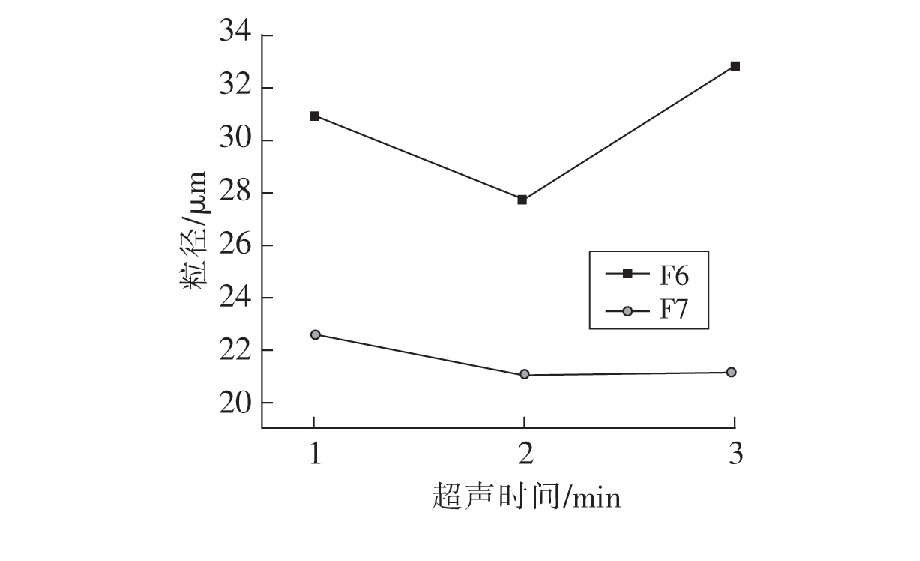
图4 F6和F7样品超声1 min、2 min、3 min的D90粒径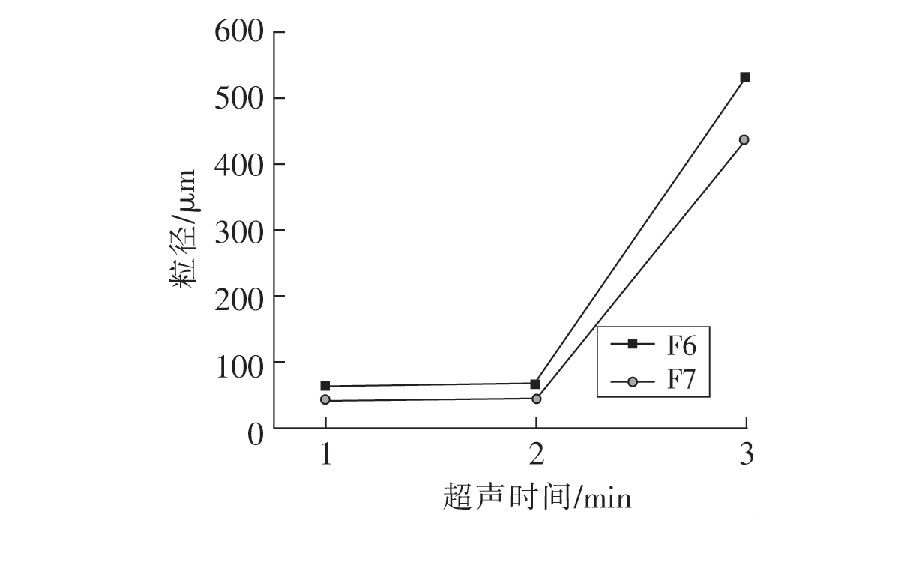
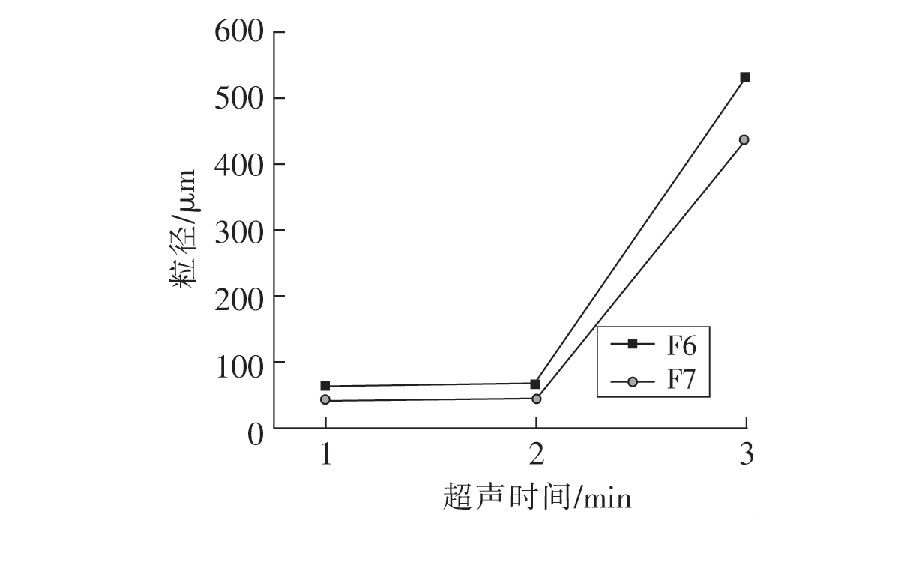
图5 F6样品超声3 min后粒径检测的微分分布

图6 F7样品超声3 min后粒径检测的微分分布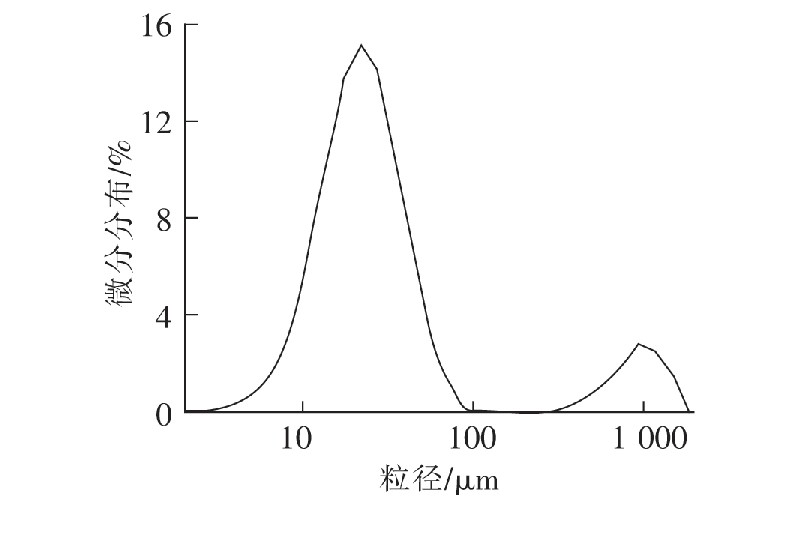
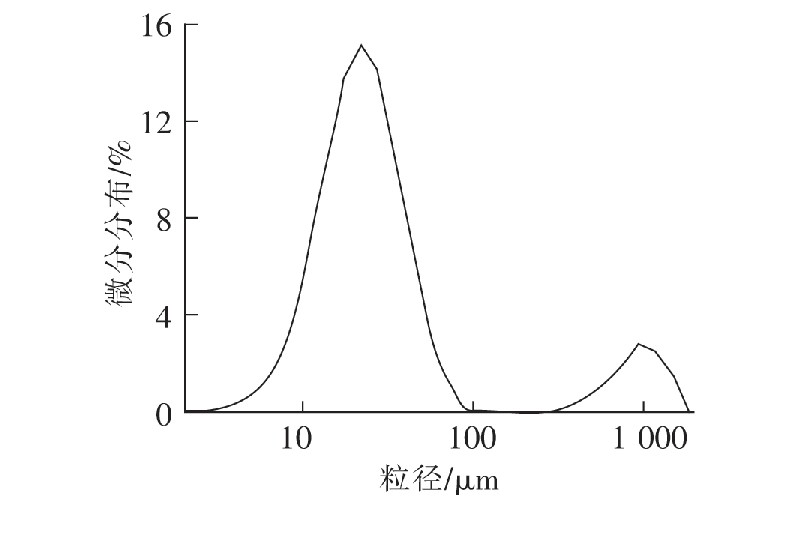
根据上述试验结果,预处理超声3 min后测定粒径数值最佳,而超声3 min后会出现数据的偏移,且石墨烯粒径目前没有相关国家检测标准,激光粒度仪也没有关于石墨烯相关测定前预处理时间的标准,根据试验数据、图线变化趋势、峰值分析,氧化石墨烯预处理超声时间3 min最准确。
2.2 激光粒度分析仪检测氧化石墨烯粉体粒径
2.2.1 测定方法
取F1、F2、F3、F4、F5、F8、F9、F10氧化石墨烯粉体样品,每种取样1 g,分别溶于300 m L去离子水中配置成溶液。检测之前使用激光粒度分析仪配备的超声装置对溶液进行预处理超声3 min,超声后对每个样品进行3次粒径检测,数据取3次测定平均值,最后将8种样品粒径测定结果绘制成图,如图7~9所示。
图7 F1样品超声3 min后粒径检测的微分分布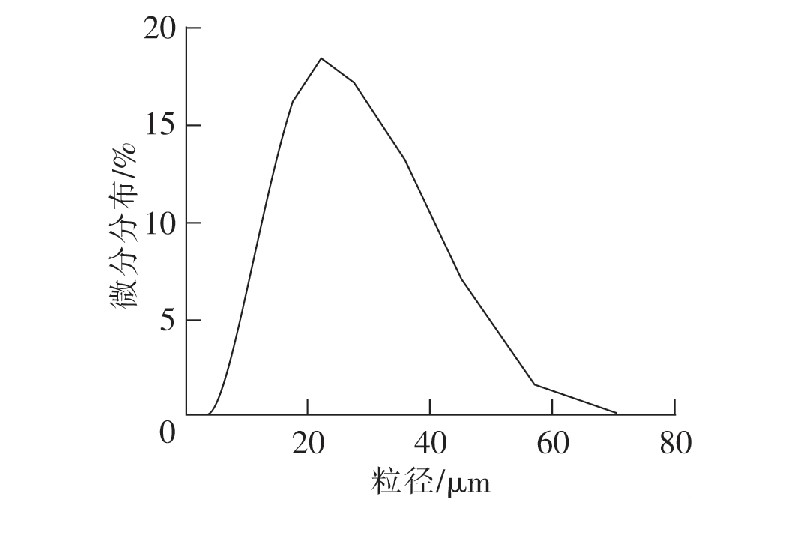
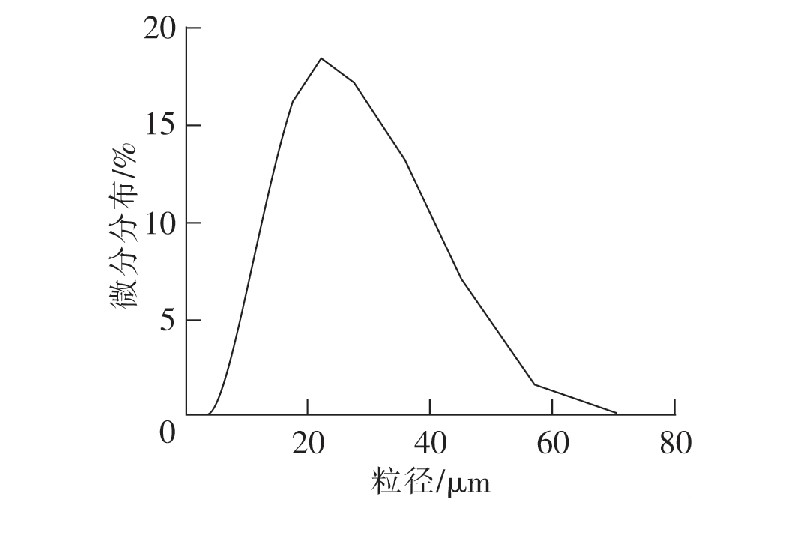
2.2.2 结果分析
图7为F1样品的粒径分布图,从粒径分布结果中可知,分布曲线呈正态分布,在3 min预处理超声后D50粒径为19.353μm,D90粒径为34.692μm。所以F1样品的平均粒径为19.353μm,且90%粒子都小于34.692μm。F2、F3、F4、F5、F8、F9、F10氧化石墨烯粉体样品经激光粒度分析仪测定后,粒度分布曲线同样满足F1样品分布趋势。图8和图9展示了8个样品D50和D90粒径数值曲线,从图中可以看出,8个氧化石墨烯粉体样品经激光粒度分析仪检测后,F4样品平均粒径最小为16.52μm,F9样品最大为23.113μm,平均粒径稳定且集中分布在20μm左右,且90%粒子粒径在50μm以下。根据试验结果可得,激光粒度分析仪测定氧化石墨烯粉体D50粒径为20μm左右。
图8 各氧化石墨烯粉体样品的D50粒径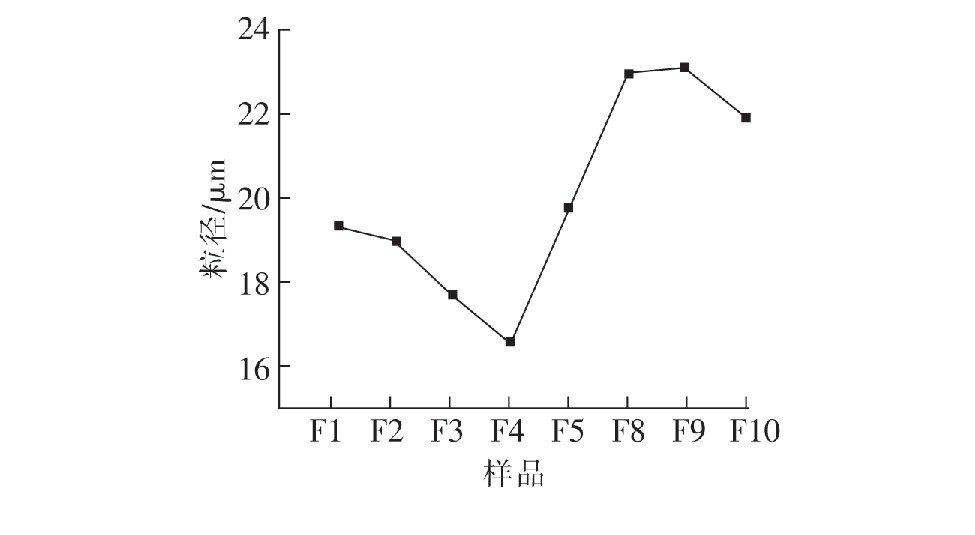
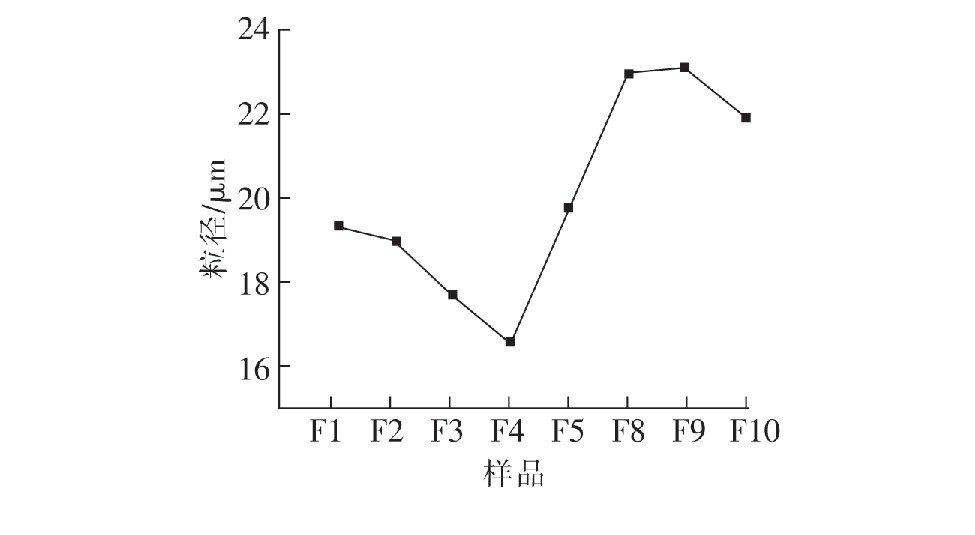
图9 各氧化石墨烯粉体样品的D90粒径

2.3 激光粒度分析仪检测氧化石墨烯浆料粒径
2.3.1 测定方法
氧化石墨烯浆料为超声工序后、喷雾干燥工序前的产品,现用激光粒度分析仪对其粒径检测,观察其粒度分布情况。试验中氧化石墨烯浆料样品为J5、J8、J9、J10,与之对应的氧化石墨烯粉体为F5、F8、F9、F10。检测前,先将浆料样品配制成与粉体样品相同浓度的溶液,预处理超声3 min。设定试验条件和方法与检测氧化石墨烯粉体时相同,再开始对浆料粒径进行检测,将测定结果绘制成图,如图10~13所示。
2.3.2 结果分析
检测结果:从图10、11中可以看出,氧化石墨烯浆料经过激光粒度分析仪检测后平均粒径为800~1 100μm,最大粒径约2 000μm。将同批次制备的粉体和浆料样品放在一起进行比较,图12、13说明了同一批的氧化石墨烯,喷雾干燥之前的浆料和喷雾干燥之后的粉体,粒径测定结果相差几十倍。
图1 0 各氧化石墨烯浆料样品的D50粒径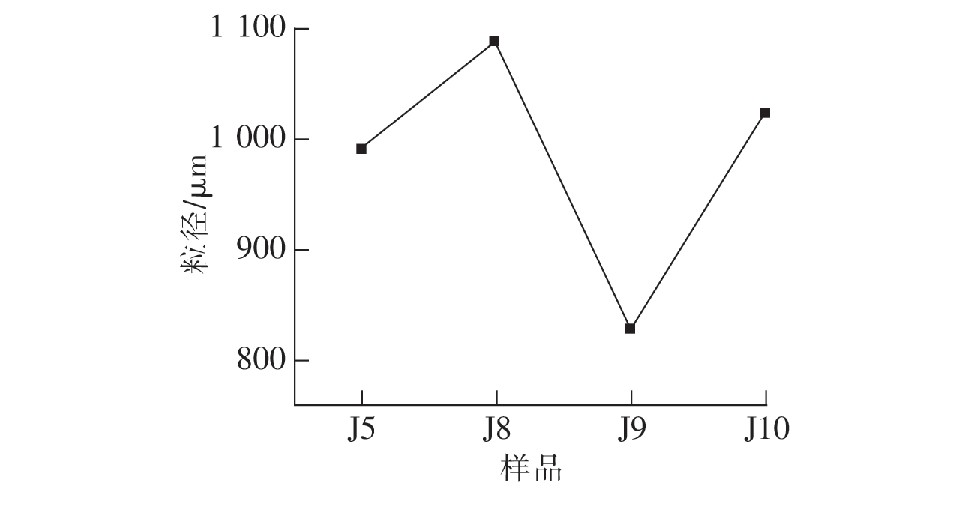
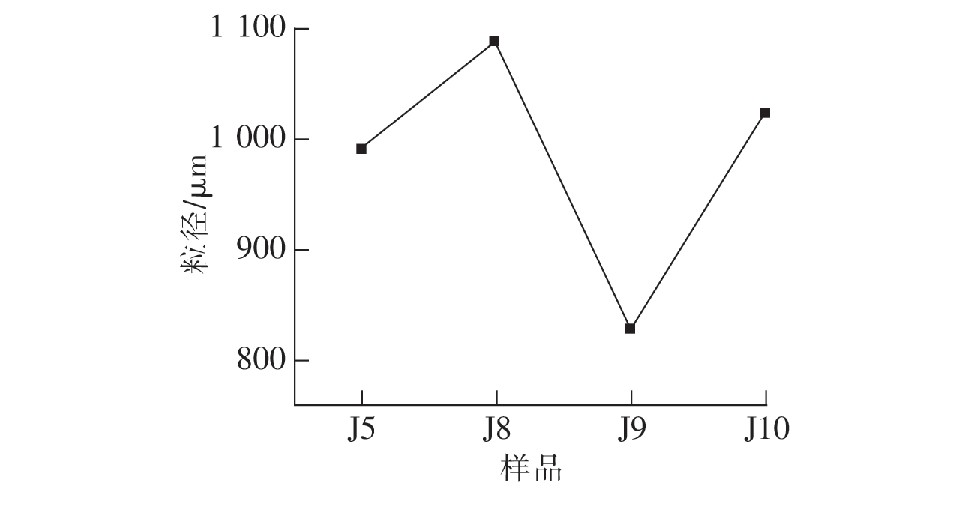
图1 1 各氧化石墨烯浆料样品的D90粒径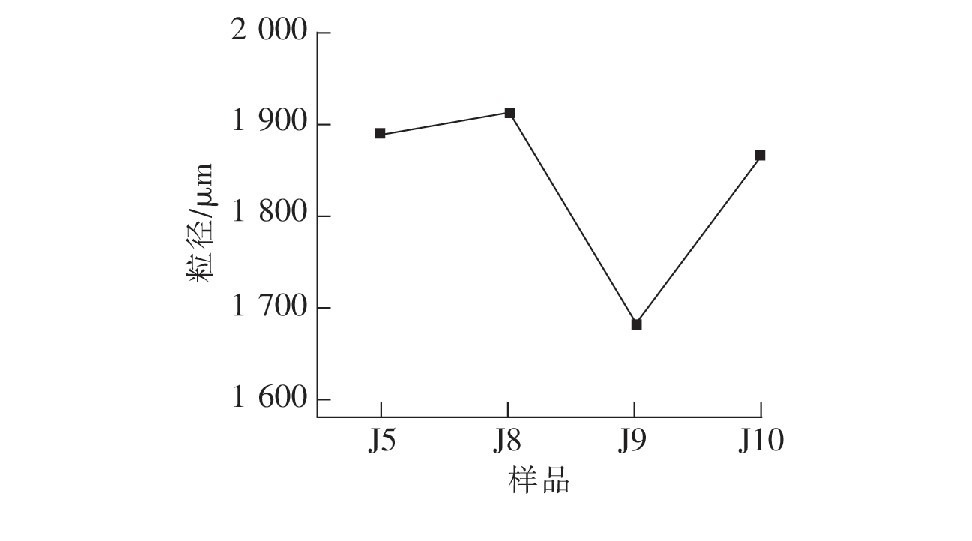
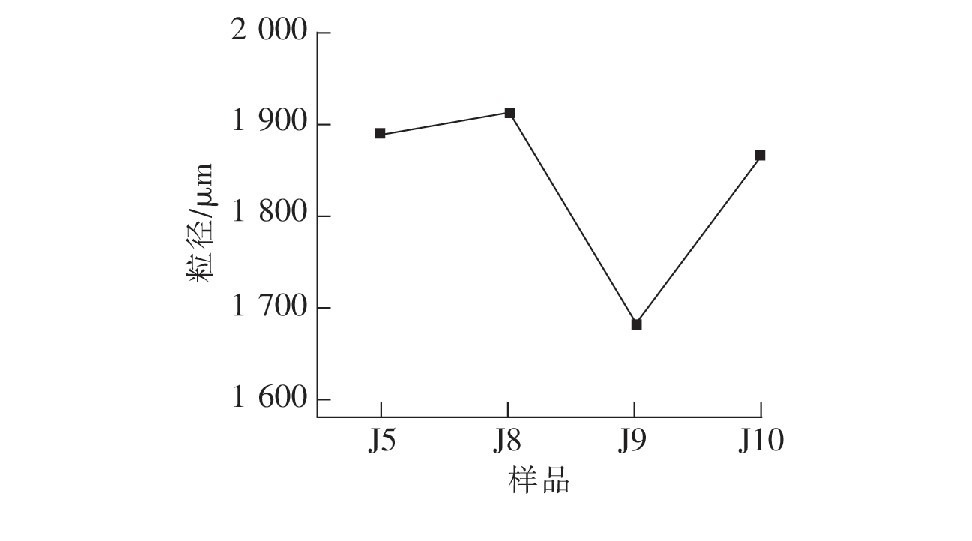
图1 2 对应氧化石墨烯浆料与粉体样品的D50粒径对比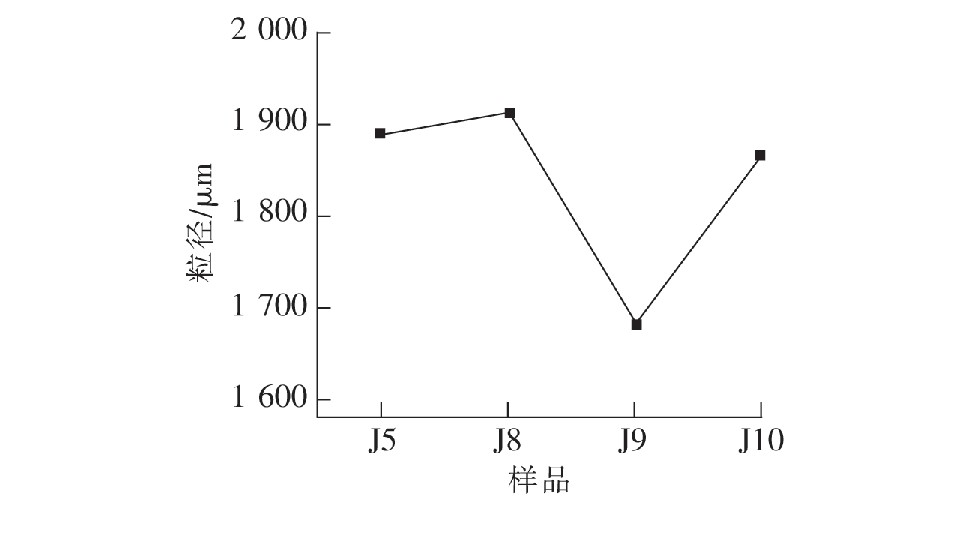
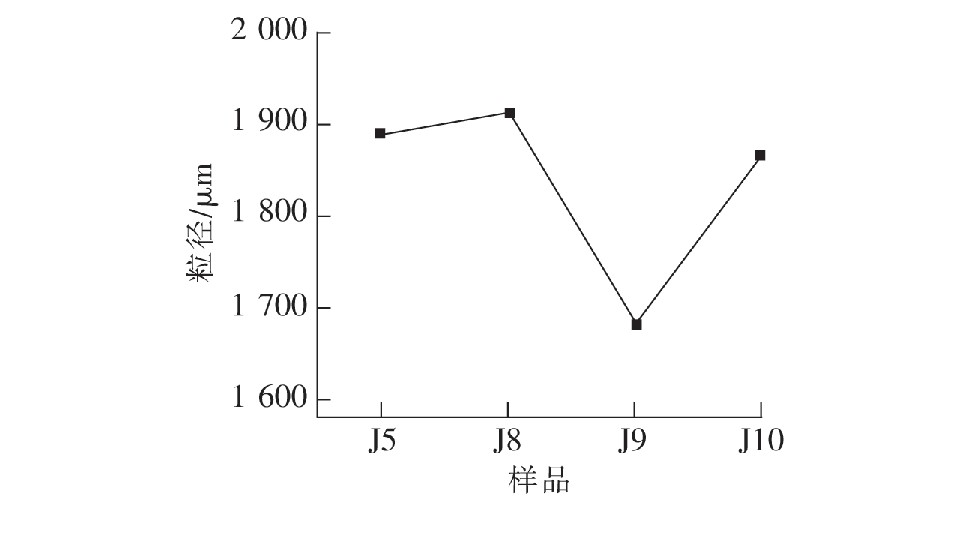
图1 3 对应氧化石墨烯浆料与粉体样品的D90粒径对比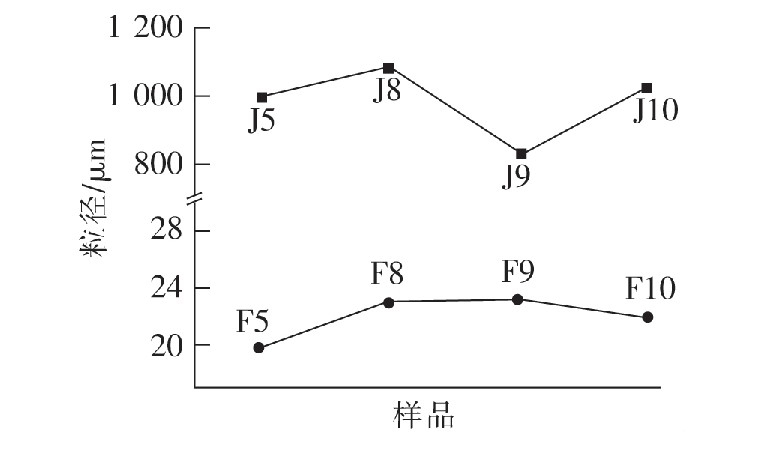
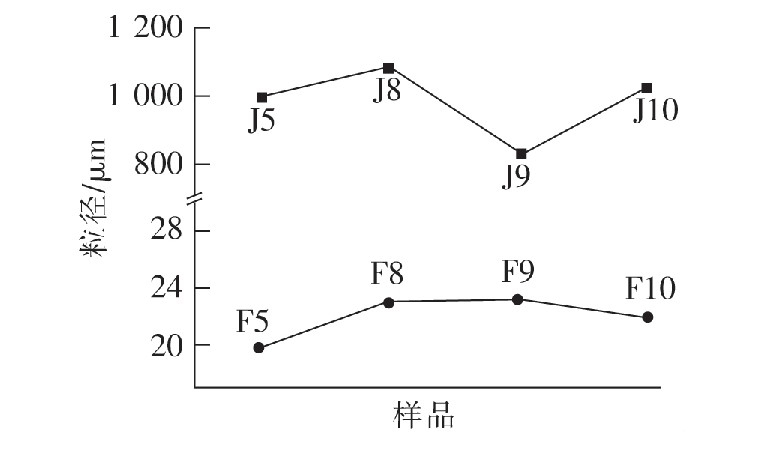
宏观角度分析误差原因:相比于氧化石墨烯浆料,氧化石墨烯粉体为氧化石墨烯浆料干燥后的产物,未发生化学变化,应与浆料性质相近,但粒径检测结果具有很大差异。毫米级别大小的粒子应肉眼可见,而在激光粒度仪检测过程中,输料管道为透明管道,试验过程中并未发现与测定结果相近的1~2 mm的石墨烯粒子。由此可知,氧化石墨烯浆料无法通过激光粒度分析仪测定真实数据。
微观角度分析误差原因:在喷雾干燥之前,氧化石墨烯呈片状,在喷雾干燥过程中,石墨烯片层受热发生卷曲,以至喷雾干燥后收集的氧化石墨烯粉体粒子呈卷曲状。氧化石墨烯浆料粒子与氧化石墨烯粉体粒子在微观形态上的区别是导致激光粒度分析仪检测结果出现巨大差异的主要原因。
工作原理角度分析误差原因:激光粒度分析仪原理是平行光在传播过程中遇到障碍物粒子,光波会发生衍射偏转,偏转的角度跟颗粒的大小相关,如图14所示。颗粒粒径越大,光波偏转角度越小;颗粒粒径越小,光波偏转角度越大。激光粒度分析仪工作中将样品模拟为一个三维球体,而单层石墨烯是一个二维结构,在仪器对样品测试过程中,单层片状石墨烯出现弯曲,仪器根据其弯曲角度可将其补充成一个球状结构,随弯曲角度越来越大,其近似球状结构的半径就会越来越小。由于氧化石墨烯浆料粒子弯曲不明显,根据其弧线近似的球体半径会非常大,由于高温干燥后的氧化石墨烯粉体呈卷曲状,其近似球体半径会大幅减小。所以,经激光粒度仪检测的氧化石墨烯浆料和氧化石墨烯粉体粒径会产生巨大差异。结果表明,喷雾干燥工序前氧化石墨烯浆料不适宜用激光粒度分析仪进行粒径检测。
图1 4 粒子对平行光的散射现象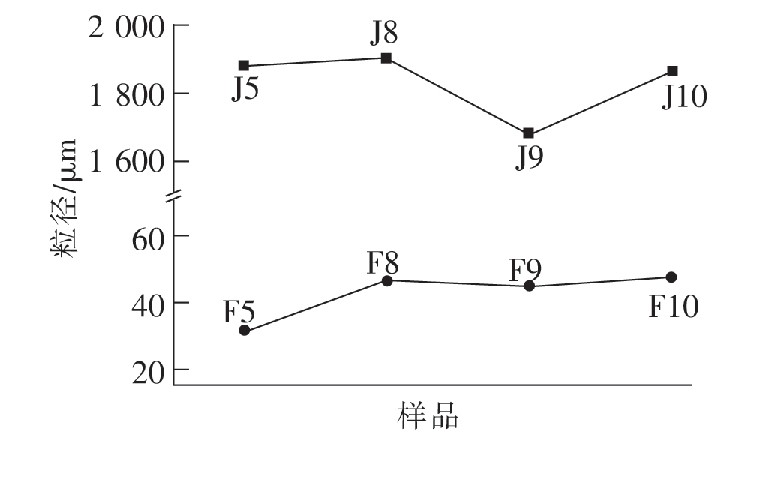
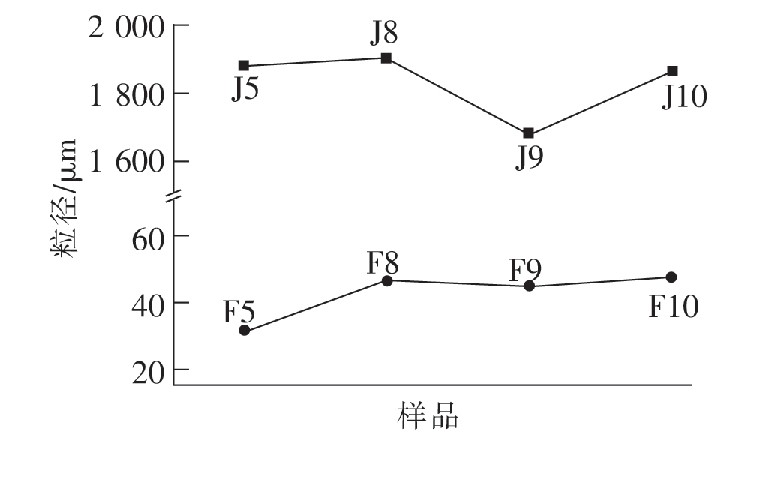
3 结论
(1)使用激光粒度分析仪检测石墨烯粒径,预处理超声时间越长,测得粒径大小越准确,但如果超声时间超过3 min,可能会改变石墨烯形貌,致使测定结果出现突变。根据数据反映情况,激光粒度分析仪检测石墨烯最佳预处理超声时间为3 min。
(2)喷雾干燥工序之前的氧化石墨烯浆料由于呈二维片状结构,不适宜用激光粒度分析仪检测。
(3)喷雾干燥工序之后的氧化石墨烯粉体,受高温后片状结构出现卷曲现象,可视为三维球状结构,因而可以利用激光粒度分析仪进行检测,测定氧化石墨烯粉体D50粒径为20μm左右。